Самый эффективный и часто применяемый способ неразрушающего контроля (далее, НК) — ультразвуковой контроль (далее, УЗК). Предпосылки появления данного метода появились еще в 1930 году, а примерно через 20 лет УЗК основным способом контроля качества сварных соединений и швов. Помимо этого, УЗК для ряда конструкций и изделии стал обязательным требованием введения в эксплуатацию.
В процессе применения ультразвукового способа контроля в изделие, при помощи специального прибора, происходит излучение УЗ-волн, которые, в свою очередь, отражаются от того или иного образования/дефекта/изъяна и возвращаются в видоизмененной форме обратно в преобразователь. Для УЗК используются ультразвуковой дефектоскоп и пьезоэлектропреобразователь. Это оборудование помогает проанализировать полученные данные, установить наличие дефекта, определить его эквивалентный размер, форму (объемный/плоскостной), вид (точечный/протяженный), глубину залегания и прочее.
Функцией выявления параметров дефектов обладает ультразвуковой дефектоскоп. Можно привести следующий пример получения данных с помощью этого прибора: при условии, что известна скорость распространения ультразвука в данном материале, можно определить расстояние до дефекта, а с помощью амплитуды отраженного импульса установить относительный размер дефекта.
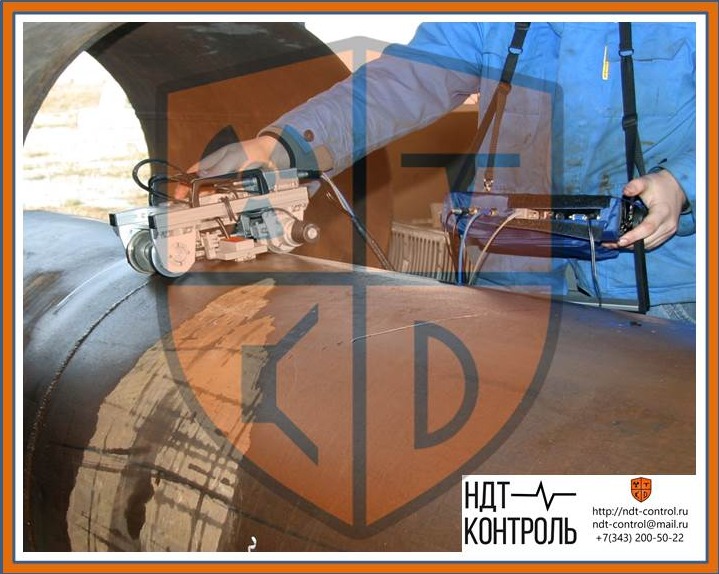
УЗК предполагает широкий перечень средств контроля. Выбор средств оборудования зависит от марки и вида материала, его толщины, геометрических параметров объекта исследования, предполагаемых/возможных размеров дефектов и так далее.
Известны 5 основных способов проведения УЗ-исследований: теневой, зеркальный, зеркально-теневой, дельта- и эхо-методы. Для осуществления УЗК стали в сфере промышленности предусмотрено использование ультразвуковых волн в диапазоне от 0,5 МГц до 10 МГц. В ряде случаев возникает необходимость в повышении частоты до 20 МГц — это помогает обнаружить самые небольшие изъяны и дефекты. В свою очередь, низкие частоты нужны для работы с объектами большой толщины (УЗК сварных электрошлаковых соединений, поковок, отливок); для контроля стали, имеющей крупнозернистую структуру и большое затухание, то есть, такие металлы, которые плохо пропускают ультразвуковые волны.
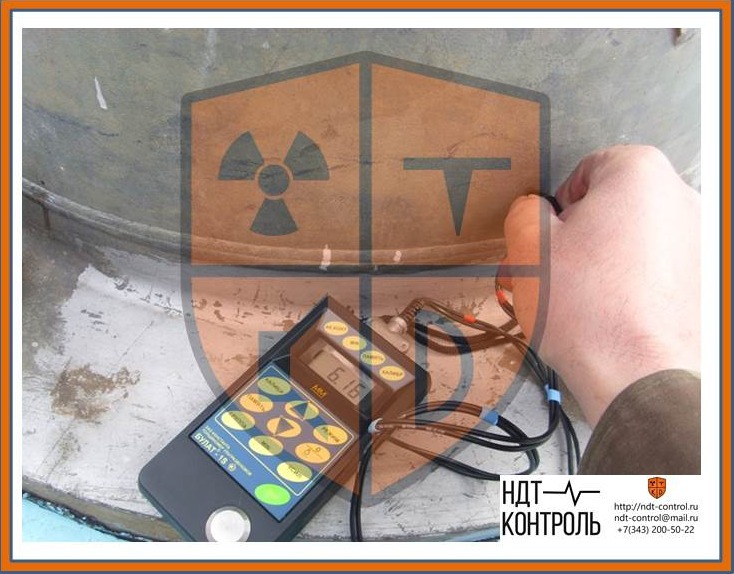
К преимуществам УЗК следует отнести:
- высокий уровень точности и скорости проведения исследований;
- минимальные материальные затраты на процедуру УЗК;
- максимальная безопасность для жизни и здоровья человека;
- мобильность и универсальность, за счет использования портативных УЗ-дефектоскопов;
- осуществление УЗК возможно на действующем объекте, без выведения и остановки работы контролируемых деталей/объектов из эксплуатации;
- ультразвуковой контроль не имеет отрицательного или разрушающего действия на исследуемый объект.
Ультразвуковой контроль имеет свои особенности и специальные условия эксплуатации. Использую УЗ-диагностику следует учитывать следующие моменты:
- УЗК не дает полного представления о реальном размере дефектов. В связи с тем, что размеры дефекта определяют в соответствии с его отражательной способностью, устанавливается только его эквивалентный размер. Допустим, в изделии имеются два реальных дефекта с одинаковыми параметрами и находящиеся на одной глубине, но один из них заполнен воздухом, а другой шлаком. Это условие поспособствует отражению импульсов различной амплитуды, а значит на дефектоскоп поступит информация о том, что данные дефекты имеют разный размер. Помимо этого, бывают такие дефекты из-за характера, структуры, формы или расположения практически невозможно обнаружить с помощью УЗК. Такие же проблемы могут возникнуть, если размер детали очень маленький, или обследуется изделие сложной формы, имеющее криволинейные и сферические поверхности малого радиуса. УЗК не дает объективного определения дефекту. С помощью ультразвукового контроля не определяется характер дефекта. Чтобы узнать характер изъяна, установить, что именно за дефект обнаружен (пора, шлаковое или вольфрамовое включения), лучше всего применять радиографический метод.
- В связи с тем, что металлы с крупнозернистой структурой обладают свойствами большого рассеивания и сильного затухания ультразвука, при УЗК могут возникнуть сложности и получить данные о дефекте не удастся.
- Необходима тщательная подготовка поверхности контроля к проведению УЗ-диагностики. Потребуется очистить поверхность контроля от загрязнений, ржавчины, отслаивающейся окалины, брызг расплавленного металла и прочего. Кроме того, должна быть достигнута необходимая шероховатость поверхностей не хуже Rz 40 и волнистость не более 0,015, в связи с тем, что даже незначительный воздушный зазор между пьезоэлектропреобразователем и объектом контроля может послужить непреодолимым препятствием для распространения УЗ—колебаний.
- Перед проведением УЗК и после зачистки требуется нанести на контролируемую часть изделия специальную контактную жидкость (гель, глицерин, машинное масло, и прочее). Это необходимо для того, чтобы обеспечить стабильный акустический контакт.
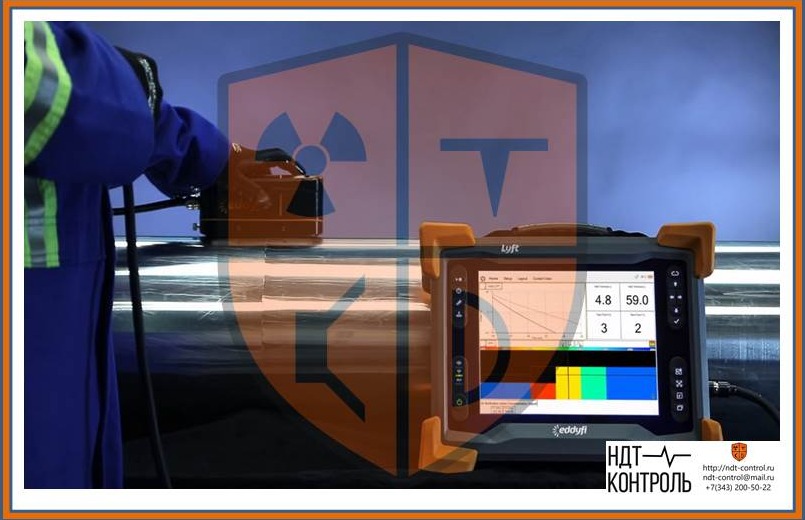
Ультразвуковой контроль считается надежным и высокоэффективным способом обнаружения возможных дефектов. Для проведения УЗК необходимы специальные знания и квалификация, то есть, осуществлять данный контроль может только подготовленный, умеющий обращаться со специализированным оборудованием и вспомогательными средствами контроля персонал. Недобросовестные производители, желая сэкономить, пренебрегают методами неразрушающего контроля, либо обращаются к УЗК только на заключительной стадии — перед сдачей объекта, когда осуществить полноценный контроль становится технически невозможно. Это может привести к аварийным ситуациям в процессе эксплуатации и даже к техногенной катастрофе. Следует своевременно производить ультразвуковой контроль и вовремя устранять выявленные дефекты.